1. Do radiators have internal corrosion protection and what is their service life?
Steel panel radiators have a high-quality external surface protection, but none of them have a specially protected internal surface. The protection of the inner surface is provided by water in the heating circuit. The oxygen contained in the water reacts with the steel surface to form a certain amount of corrosion. After the corrosion reactions are completed, all the oxygen in the circuit is consumed and the corrosion process stops. It is very important that the system can be vented without any problems and that the circuit is not refilled and drained unnecessarily. The service life of steel radiators is closely related to its correct design and operation. In order to be as high as possible, we unequivocally recommend the installation of closed systems without the risk of introducing oxygen and other air gases into the circuit. Properly operated, steel radiators can last for 30 years or more.
2. They can be panel radiators installed in bathrooms?
Conventional steel panel radiators are not designed for humid environments. Their corrosion resistance at ambient humidity above 70% is significantly reduced. For this purpose, galvanized radiators have been developed. These radiators do not differ from outside in any way from normal production. The electrolytically applied zinc layer is hidden under a polyester coating in shade RAL 9016. The range is narrowed down to models without convector plates due to the achievement of maximum corrosion resistance. More detailed information about galvanized radiators can be found in the Products section.
3. How do I keep my radiators from freezing?
If we do not want or cannot use the heating system during the entire heating season and for economic reasons we do not even want to temper it, it is necessary to fill this system with antifreeze. There are antifreeze mixtures designed for this purpose. We fill the open system with these preparations simply through the expansion vessel. Closed systems can be filled after partial or complete draining of the circuit, for example via the highest point (automatic vent valve or directly into the radiator). It is important to maintain the prescribed ratio of water to antifreeze and to allow the circuit pump to run long enough after refilling to ensure perfect mixing. When filling the system with antifreeze, it is necessary to consider the reduction of the heat output of the radiators due to the decrease of the specific heat capacity of the heating water. See the following table for approximate values.
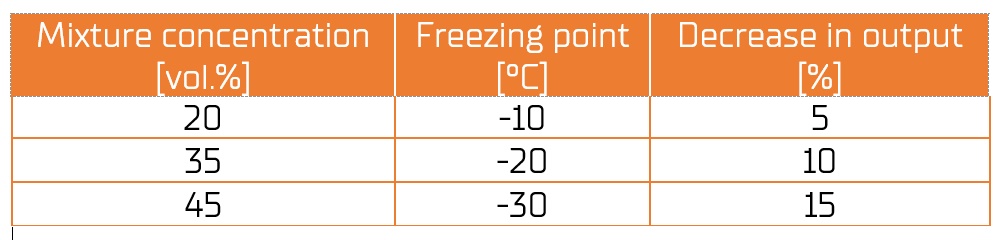
4. What is the problem if the radiator does not heat or is warm only in part?
Here can be several causes for this phenomenon. The first is an oversized radiator. This happens when the estimate of heat losses is wrong, or if there is a change in the thermal insulation properties of the building structure (insulation). In this case, the installed body must supply significantly less heat than it is capable of. It’s similar to a slow ride on a powerful car. This cause can be ruled out if it is cold in the heated space when the body is slightly warm. The probable cause is insufficient flow, which can result either from incorrect installation of the radiator (long distance from the main branch) or incorrect presetting of the thermostatic valve. In any case, contact your building administrator or plumbers.
5. What causes noise in radiators?
The heating system is often a source of noise, which has different forms and therefore different causes. However, the cause of the noise is almost never the heater itself.
If it is a sound like splashing or plopping of water, it will probably be a bad deaeration of the radiator. Each radiator should be equipped with its own vent plug and be properly sloped. The vent should be at the highest point, on the opposite side of the valve. In older systems, the venting of radiators is solved by the opposite arrangement of bodies, which means that the highest point is at the point of connection – at the valve. The air thus could escape into the riser and leave the system at the highest point. New control valves controlled by thermostatic heads usually create a greater air barrier than conventional shut-off valves. With a larger volume of air in the body, for example when refilling system after repair, degassing is then quite lengthy and often not 100% successful. We can help by partially loosening the valve thread and thus releasing the trapped air. It is not good to neglect the venting of radiators. In addition to the decrease in heat output, there is also an increased risk of corrosion.
Roar or hissing occurs very often. It is caused by a high pressure difference on the control valves. The valves shut off the flow of water to the radiators depending on the setting of the thermostatic heads. When closing the valves, the flow cross-section decreases and thus the pressure difference in front of and behind the valves increases. This increases the flow rate of the fluid through the valve. A properly designed system must respond to such pressure changes and compensate for pressure differences through the control valves on the risers. If this is not the case, there is an unpleasant hissing sound, which can be very unpleasant and disturbing, especially at night. Noise can be further intensified if the heating water contains air bubbles. Sometimes a larger opening of the valve is enough, other times the noise will not disappear even when it is opened to the maximum. Expert intervention is required to eliminate this phenomenon. Many times it is necessary to change the differential pressure compensation system.
Knocking, ticking, or squeaking are sounds that are most often caused by thermal expansion of the supply line. The pipe expands during heating and contracts when cooled. If the passages between the floors or rooms are without the possibility of free movement of the pipeline, a tension is created, which ultimately causes noise. This can happen on ascending pipelines or even branches for connecting individual radiators. Due to the opening and closing of the valve during regulation, the pipe temperature changes. Remediation is not usually easy. Already during the construction work, it is necessary to consider the expansion of the pipe and allow it to move freely. An additional solution to the situation lies in the location of problem areas and the subsequent removal of fixed pipe bearings and filling them with flexible bearings. In the case of radiators, a partial solution is the use of brackets allowing movement in the horizontal direction.
Whistling or clattering may be a sign of a fault in the radiator connection. This happens when the radiators of the Ventil Kompakt (VK) type are connected in the opposite way. The exchange of the supply and return can easily occur, especially when installing radiators with right and left connections on one branch at the same time. The position of the inlet and return changes in a mirror image. In general, the return (outlet) principle is always closer to the edge of the radiator. When connected in the opposite direction, water enters the integrated control insert from the opposite side, which results in oscillation of the valve cock plug associated with sound effects. The intensity and nature of the sound varies depending on the flow rate and the working pressure in the system. At the same time, the opposite connection has a negative impact on the heat output, which drops by about one third.
6. What water to use for the heating system?
The question of the required properties of heating water is asked very often. Water quality affects the operation and service life of the entire heating system. Drinking water is usually used as the filling medium. The fact that water is classified as drinking water does not guarantee its suitability for heating systems. Important parameters are hardness, acidity, salt and dissolved gas content.
Water hardness is related to the geological subsoil and soil conditions. In higher positions with a granite base, the water tends to be softer, in lower positions it is harder due to limestone rocks. The hardness of water determines the amount of calcium and magnesium salts contained in water. During the operation of the system, these salts form insoluble carbonates – limescale – on the heat exchange surfaces of the boilers. These are usually boiler exchangers. The layer of limescale can grow on these surfaces and over time it peels off and spreads into the system, where it causes clogging of individual fittings. The result is not only a decrease in boiler output but also the gradual decommissioning of control valves. In addition, the formation of limescale releases carbon dioxide into the water, which is corrosive and at the same time enriches the system with unwanted gases. Such a system must be constantly replenished with additional water. This cycle of topping up and clogging the system with limescale ends with the clogging of the exchanger, resp. valves.
The hardness of water is determined, for example, on a German hardness scale (° d or dH °). On washing powder packages, it is often divided into 4 stages:
1 | 0 – 7 °d | soft |
---|---|---|
2 | 7 – 14 °d | moderately hard |
3 | 14 – 21 °d | hard |
4 | over 21 °d | very hard |
Water with a hardness not exceeding 5.6 ° d is suitable for heating systems. Other matching units can be listed for comparison:
German °d | French °f | English °e | American gpg | mmol / L |
---|---|---|---|---|
5,6 | 10,0 | 7,0 | 5,8 | 1,0 |
Your drinking water supplier should also provide you with the water hardness value. The hardness of the water can be measured as a guide, for example, using test kits for aquarists. These can be based on indicator papers or on special preparations (methyl orange), which are added to the liquid sample dropwise until they change color. Each drop represents, for example, 1 ° d. However, we recommend leaving the water treatment to specialists. It is always cheaper than paying later to repair the damage to the system.
An important factor influencing the corrosion resistance of the heating system is acidity – pH. Due to the instability of the chemical bonds of water, its chemical composition and thus its acidity can change under certain conditions. Neutral water has a pH value of 7. The lower the pH value, the more acidic the water and, conversely, the higher the pH value, the more alkaline it is. For heating water, it is necessary to adjust the pH value according to the resistance of the materials used in the heating system. The pH value can be measured e.g. using indicator papers.
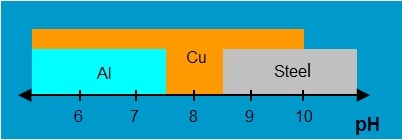
Despite the fact that for a system with different materials such as steel and copper, we choose a pH that is as gentle as possible in terms of corrosion processes, for example, electrochemical corrosion can occur. This is caused by the high salt content in the water, also referred to as salinity. Salinity, or rather mineralization, is the sum of all salts dissolved in water. These are mainly cations Na+, K+, Fe+ and anions Cl–, SO42-.
Their content in water can be specified by conductivity. Conductivity (ion content) is given in µS (microsiemens) and is measurable with a conductometer. Water with a conductivity of up to 0.5 µS / cm is suitable for heating systems.
The gases are dissolved in water. The heating water is mainly nitrogen, oxygen and carbon dioxide. The content of dissolved gases in water depends on its temperature and pressure. The solubility decreases with increasing temperature and decreasing pressure. This phenomenon is evident when opening a bottle of carbonated beverage. A sudden drop in pressure causes carbon dioxide bubbles to appear, which have so far been dissolved in water. In nature, water at atmospheric pressure normally contains dissolved gases, namely oxygen up to 11 mg / l and nitrogen 18 mg / l. Although nitrogen is an inert gas, its larger amount in the system leads to circulatory disturbances. Seamless nitrogen concentrations in water must be less than 15 mg / l. Oxygen and carbon dioxide are the biggest threats to the heating system. These gases cause system corrosion. Much of the gas can be removed from the system by venting. Of course, this cannot be done 100%. Residual oxygen and carbon dioxide are consumed in corrosion reactions that stop over time. However, if oxygen continues to enter the system, this is the most common cause of system corrosion.
1g of O2 corrode the 2,6 g of Fe to form up to 4,13 g of Fe(OH)3, i.e. rust, with the simultaneous formation of 1,4.10-3 m3 of hydrogen.
The source of oxygen penetration can be leaks of individual elements of the system, unsuitable or poorly designed expansion vessel, permeability of some plastic elements, but above all it is replenished water.